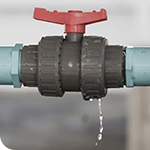
James Yerke, PE, CEM, Section Manager and Senior Associate at SSOE Group, was featured in this Food Engineering Magazine article that discusses inefficiency and loss/costs caused by physical leaks within a facility, namely air and water, and different tools available to find them and fix them. Leak problems will exacerbate further as time goes on, increasing costs if not corrected. When it comes to leaks, it’s in your best interest to dig into the issue before the issue digs into your bottom line.
According to the U.S. Department of Energy, the average facility is losing approximately 30 percent of its compressed air to leaks, with half of those facilities making very little effort, if any, to correct the issue. In addition to providing tools and technologies to assist in unveiling these leaks, this article tallies up the cost associated with leaks and the savings that can be acquired by fixing them. Yerke suggests measuring and recording pressure and flow rate data, reviewing changes and trends. This will help determine if a leak exists, with an IR imaging system noted as a choice solution in the challenge of finding it. Yerke also recommends quantifying energy loss by calculation using variables such as the bin method, using an IR thermal camera to glean qualitative information.
Is it more economical to find energy leaks yourself or call in an outside service? The answer: Compressed air savings usually start at $10,000 per year and can go as high as $50,000 per year. Hiring an expert energy consultant such as SSOE can quickly deliver value, typically providing continuous, long-term savings that outweigh the fee.
To read the full article, click here.