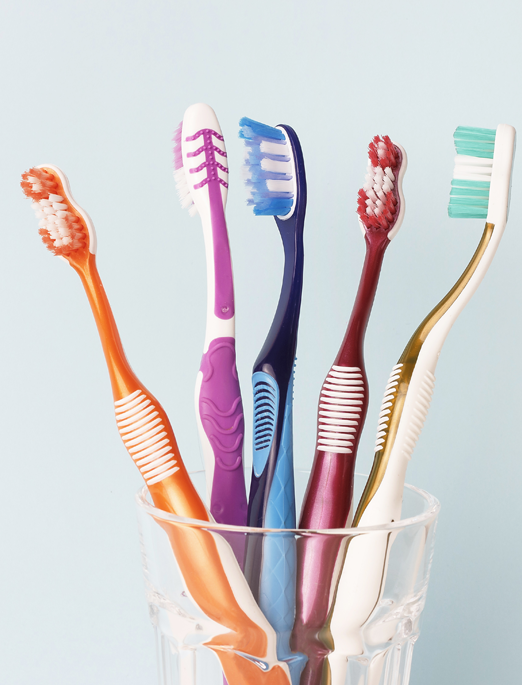
Since 2009, SSOE has documented savings of over $20.1 million on projects for this client.
When this consumer products client identified the need to increase production, they called on SSOE to lead the design, OEM coordination, and installation as part of an EPC project delivery solution. We were selected based on our pre-determined capabilities in safety, innovation, cost, and success on previous projects.
The plant required facility work to accommodate the new equipment, including overall design for layouts, facilities, mechanical, and electrical. Design services included 3D scanning of areas proposed for the new equipment to develop engineering packages to perform construction activities.
The major scope of this project consisted of process equipment installation and upgrades to the plant’s central material delivery system. Support services included new equipment foundations, electrical and control circuitry, and balance of plant mechanical services. The most challenging aspect of this project involved placing the equipment in an older section of the plant with limited ceiling clearance.
The client provided SSOE with older scans of the areas that were not up to current quality requirements. Instead of re-scanning these areas, SSOE was able to supplement the existing data with portable scanning at the site, which ultimately contributed to a detailed 3D design. This augmentation of additional higher quality scan data provided better insight to the team and contractors as we developed the vendor models. SSOE completed this scan augmentation with our own project personnel and portable scanner, which saved the project time, trouble, and money, versus hiring a third party to travel to the site, complete safety training, and re-scan the entire area.
SSOE’s construction-level coordination included pull-planning sessions with the owner and contractors, and use of the NavisWorks model on a daily basis. This highly detailed design also allowed SSOE to conduct specific coordination meetings with the following user groups that were not directly involved in the project to minimize rework after installation:
- Operations – Locate accessories, verify forklift access, and locate operator stations and PLC locations.
- EH&S – Verify exact location of LOTO points, review fall protection strategy, and design machine guarding.
- Bridge Crane Manager – Bridge crane, including lift dimensions.
Central Materials – Review staging areas and lay out central product delivery equipment.