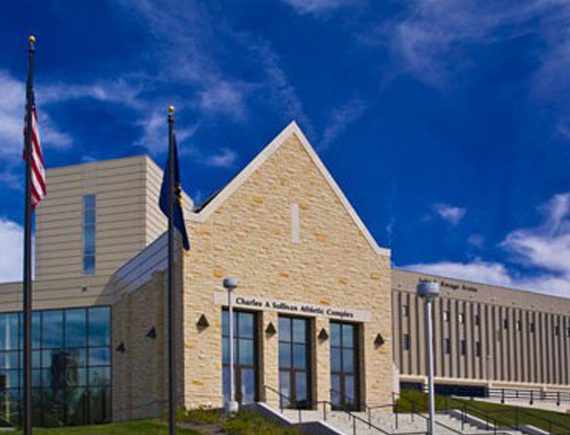
75% of the existing building envelope and 50% of interior, non-structural elements were maintained saving the client construction costs.
Savage Arena, located in the heart of the University of Toledo’s main campus, was renovated and expanded to transform the arena into a state-of-the-art facility for student athletes and fans.
The 163,000 SF facility features numerous amenities for student athletes and fans, including a new entry pavilion; the Wall of Champions and Hall of Fame; improved locker, weight, and training room facilities; specialty seating, including 12 suites, 17 loges, and 194 club seats; 13 concession areas with 34 points of sale; and a pro shop selling Rocket apparel.
Keeping with the university’s mission to be a leader in sustainability, the facility is LEED® Gold certified. Other efforts to minimize environmental impact included reducing water consumption by 20% through the use of landscaping materials that require little to no irrigation, installing low-flush toilets, and using certified wood and recycled content materials throughout the facility. Meticulous construction management allowed for more than 50% of construction waste to be diverted or recycled.
This renovation also included the transformation of the existing Savage Arena lower level from racquetball courts to a steam generating facility for the entire campus, requiring installation of a 90-foot tall stack in a 25-foot deep areaway.