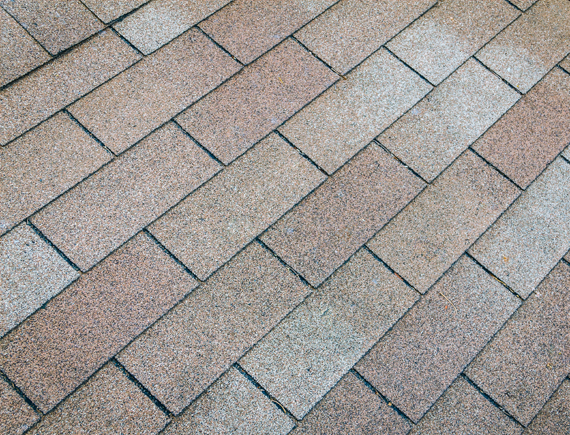
SSOE suggested the use of steel eccentrically braced frames in lieu of ordinary steel moment frames on a new building in a seismic zone saving the client $80,000.
A long-term client enlisted SSOE to design a laminator addition that would enable them to manufacture a new shingle product. This involved reconfiguring the shingle manufacturing process and designing a building to house the new equipment.
The strategy included two major phases: Phase 1 included relocation of the existing packaging system equipment to make room for the new laminator. Phase 2 included the installation of the new laminator and auxiliary systems. SSOE engineered and designed extensive controls to handle process changes to the granule, asphalt, and new laminator system.
The expansion also involved joining a manufacturing facility on one property to an adjacent warehouse facility that was owned separately. Electrical service had to be fed separately to the two adjacent sites and underground piping for a fire main rerouted. SSOE provided architectural, structural, electrical and process controls design, and upgraded the alarm system and fire protection for the expanded facility. The team assisted the client with attaining permits and installation and commissioning of equipment.
SSOE fast-tracked the project in order to meet the client’s schedule for plant start-up and manufacture of the new product.