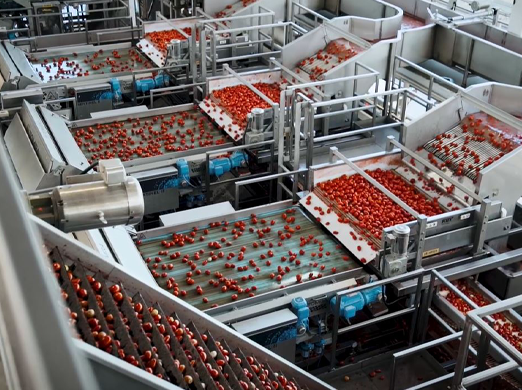
SSOE was selected to act as the Owner’s Representative for this long-time food client on an important tomato sorting and processing project. Working closely with EC Nelson, the project’s Design-Build mechanical contractor, along with the electrical and integration contractors, SSOE provided design quality assurance and managed all aspects of the project on behalf of the client. The project was completed on schedule, in time for the seasonal arrival of tomatoes. The new electronic system sorts unpeeled tomatoes by quality and color, sending a larger percentage of high-quality tomatoes to the process lines making high-end diced tomato products, while directing the lesser-quality tomatoes to the evaporators to be made into tomato paste. The new process handles 280 tons of tomatoes per hour.
As the Owner’s Representative, we managed a multitude of moving pieces (designer, contractor, equipment manufacturers, purchasing team, project controls team) that needed to align at just the right times for successful project execution. SSOE also managed the master schedule, which included the engineering packages release timing, equipment ordering, the completion of programming, equipment testing, safety checks, and performance validations. Project team meetings were held weekly along with multiple meetings throughout the week to make sure project milestones were on track, and project status reports were delivered directly to the client’s upper management team. Additionally, we worked closely with Procurement to develop and process requisitions for purchase orders to support construction tasks as needed, while handling all administrative project-related tasks.
Key to the success of this project was our ability to be adaptable as we faced project challenges outside our control. Adjustments made included compressing the schedule when needed and sometimes having crews on-site around the clock. We utilized a combination of our Owner’s Representative and added an additional SSOE resource to shoulder the on-site night shift Construction Manager role, which ultimately reduced the schedule by a week and a half.
In March 2020, restrictions were implemented due to the world-wide Covid-19 pandemic, adding unforeseen project complications. At this time, we were tasked with providing a safe, Covid-free working environment, monitoring the ability of the client-ordered European equipment to be delivered to the U.S., and developing a solution to get key project staff located around the U.S. to the client’s site when needed. Solutions included the development of on-site safety protocols, which included mask wearing, taking temperatures, and completing health questionnaires. Most importantly, the client dedicated a several company jets to move critical resources to and from the site, including the Owner’s Representative and other key personnel. This helped ensure the project was completed in time for the July 1st arrival of tomatoes from the local farmers.
To meet the client’s deadline while completing the project safely, the roof was installed at nighttime during off-shift hours. SSOE’s on-site Owner’s Representative pulled double shifts until another SSOE resource could be brought on-site. This allowed the project to complete on time, saving the client $3,198,000.00 in production cost if all work had been limited to one shift.