Revolutionizing Technically Complex Project Execution in Mexico with EPCM
by Erick Kuri, Mexico Business Leader and Operations Manager
The use of EPCM (Engineering, Procurement, Construction Management) has emerged as an effective way for leaders in the United States and Mexico to optimize project delivery.
Taking the EPCM approach requires a mindset shift, as the EPCM team assumes more ownership for the duration of the project.
In a traditional project, the design team participates in creating drawings and providing all the information required during the design phase, and then hands off the completed design to the contractor, who is responsible for tracking down the materials and construction specified in the design.
In an EPCM project, by contrast, the architect / project team is responsible for the project up through the construction phase.
If anything specified in the design is unclear, ongoing operations are at stake, or a highly technical solution is required, the project team (and in some cases, the owner) is responsible for resolving it.
In other words, the responsibility for both design decisions and execution fall to the same group of people, which streamlines the process considerably.
Up front knowledge of this challenge and a plan to solve it is invaluable for companies in the U.S. and Europe looking to expand their global footprint by investing in Mexico. Here are insights.
Context in Mexico Today
Assurance. A major corporation with a growing presence in Mexico is focused on functionality and cost in the planning and construction of new distribution centers. And, leaders are making the necessary investments for enhanced functionality while remaining mindful of cost.
With EPCM, the same concerns exist, but the process offers inherent assurance. While stakeholders assume some challenges related to doing construction in Mexico, they seek high-quality projects through experienced teams.
With the EPCM process in place to ensure adequate oversight, the construction process has integrity that allows the team to take over, and decision makers can expect defined results with minimal involvement.
Value of an EPCM approach. For companies that are making initial steps to expand into Mexico, stakeholders find tremendous value in having a project team utilize an EPCM approach as a means of getting the contractor and the architect engaged collaboratively from the very beginning of the project.
This is an unusual approach for a project in Mexico, as opposed to other global marketplaces. In a conventional project approach in Mexico, the architect delivers construction documents with no subsequent involvement.
From that point, a contractor can apply various bidding strategies, often providing a cost-competitive initial bid. However, at that very early stage decision makers cannot see the profligate overruns and additional funding requests in the field, with stakeholders having few alternatives as such issues arise.
Proactive EPCM approach pays – from site selection through construction. An EPCM approach works well because it empowers decision makers to proactively organize and manage the financial components of the project including site selection, planning, design, engineering, construction team selection, as well as construction.
The topography of various regions of Mexico can come as a surprise to corporations that are investing in land from a distance, and local contractors aren’t always aware of the need to offer education and insight.
One notable example occurred when a large corporation inadvertently bought a site for their first Mexican facility that was essential swampland, and incurred additional expenses related to securely anchoring the buildings.
Had an experienced team been involved earlier, project team leaders could have steered stakeholders toward a better site, with substantial knowledge about the best industrial zones throughout the country and their incentives, logistical advantages, and workforce considerations.
3D modeling sharpens EPCM execution. 3D modeling has been a game changer for project delivery in general, but in Mexico, its increasing popularity has sharpened EPCM project execution in particular.
To be able to use the same model from design through construction, an experienced team can combine the functionality of the model with their inherent knowledge about contractors in the area who have a level of expertise and a sufficient technology background to undertake such a project.
This level of accuracy is unattainable through other product delivery approaches, especially design-bid-build, which lose the level of collaboration between contractor, architect, and owner early in the project. This loss can be measured in project schedule delays and increased costs.
If the contractor and design team are aligned, when late-stage changes are made during construction, the model can immediately be updated so that the model is completely reflective of the final product in the field—an invaluable resource.
Quality is Key in Mexico
Quality verification. Without the level of oversight other countries enjoy, corruption is unfortunately possible in construction.
For example, contractors may sell more expensive materials, such as a carbon steel pipe, but construct with plastic pipe when not under observation. The sooner owners can be made aware of this risk, the better they can prepare for and mitigate it.
Quality verification is presented to owners as a means of resolving such challenges and EPCM provides the distinct advantage of ensuring quality. The team can offer correct specifications and ensure the contractor is constructing as specified. And, with EPCM, there is more opportunity for the engineering partner to have local involvement and oversight.
On-site assurance from around the globe. This additional layer of assurance is especially important for stakeholders in an offshore situation who may feel powerless to control on-site activity.
Companies are concerned with maintaining good practices—not just in terms of safety but in accordance with ethics, including the Foreign Corrupt Practices Act. The value added by experienced teams to provide quality assurance by directly partnering on-site with foreign investments is substantial.
When the responsibility rests with the same party throughout the project, the continuity guarantees leaders the correct execution of the project in full. The same team takes the lead in all phases, acting on behalf of stakeholders to do the best engineering and the best procurement at the best prices.
Project team offers authority with EPCM. With the design-build approach that is typical in Mexico, the construction firm bids for the project and they receive funds to build, with design taking place essentially in tandem with construction.
This approach is popular for stakeholders who have urgent schedules but can be problematic when the construction entity makes adjustments in the field, losing an aspect of the design integrity with each change order.
In the EPCM approach, the project team becomes the final authority on design, construction, and quality assurance.
Advantages
Cost. From the owner perspective, the consolidated approach requires fewer resources, providing a distinct cost advantage. In design-build, the owner must provide supervision to contractors, resulting in multiple layers of oversight.
This is not necessary in EPCM, when all the responsibility for project execution is on the same team.
From the budget perspective, that responsibility means that owners can maintain the budget they commit to at the beginning of the project, which provides a huge advantage in both short-term and long-term planning.
The combination of design and procurement by the same EPCM team means many of the details can be set in stone earlier than they would be if the design were preliminary with decisions left to the contractor.
Finally, the oversight provided in EPCM, in terms of on-site control and monitoring of construction ensures that the project does not go over budget due to surprises late in the project.
Gaining global popularity. Project delivery in Mexico has traditionally been a design-build or design-bid-build arrangement. In Mexico today, EPCM is more the exception than the rule, but its popularity in the global economy is increasing its reach.
For an owner looking to invest in a site in Mexico and building a new plant, the advantages in cost and schedule for the overall project are well worth the initial investment of time to assemble the team and perform the detailed engineering.
The mindset of experienced project teams is different as well: they view their deliverable not as a set of construction documents, but as the building itself.
Design is not complete until the keys are turned over and the building is in the hands of the decision makers. The ability to provide such a solution is a major differentiator in a market where that is a rarity, thereby revolutionizing project execution in Mexico with EPCM.
Ing. Erick Kuri is the Mexico Business Leader and Operations Manager at SSOE Group (www.ssoe.com), a global engineering, procurement, and construction management firm. With nearly 20 years of in-country experience as a manager and engineer, Erick has extensive project knowledge with automotive / manufacturing facilities and distribution centers in dozens of cities throughout the Mexican industrial corridor. In addition to having local resources and knowledge of the Mexican construction market, Erick is able to execute projects more quickly and more cost effectively for SSOE’s clients. He can be reached at 52.477.391.0420 or by email at erick.kuri@ssoe.com.
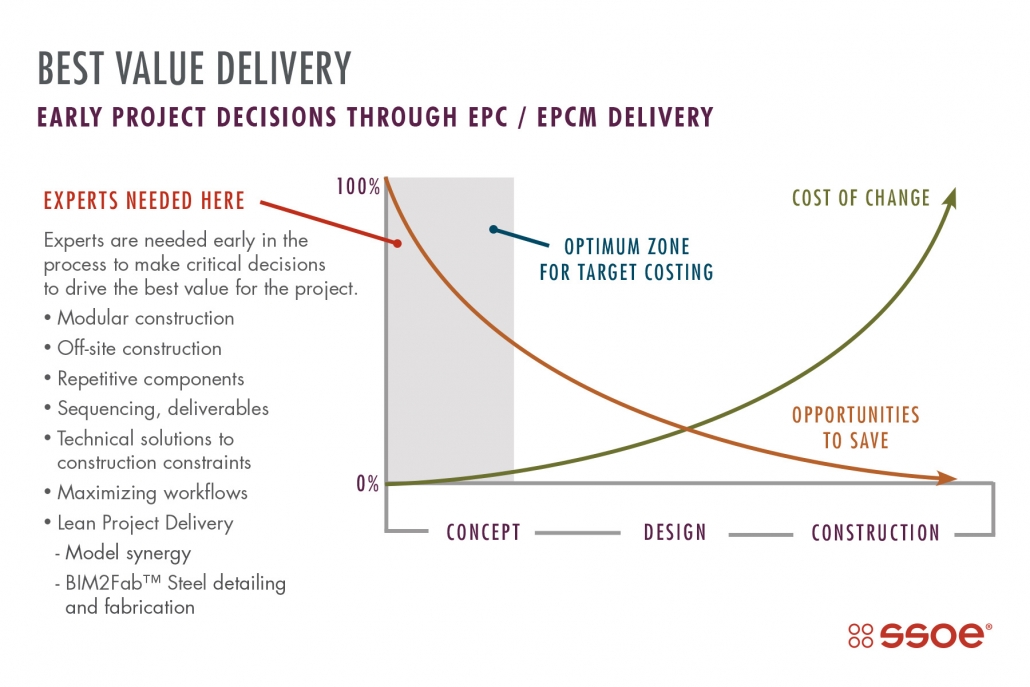